Printing and packaging industry environmental protection ink, special ink type you really understand?
Time:2023-02-01
Views:4098
Special ink belongs to anti-counterfeiting ink, it is the basis of anti-counterfeiting ink. Can be used in packaging, advertising brochures, publications, etc. Major printing methods, such as offset printing, gravure printing, flexo printing and screen printing can be implemented in pearlite printing.
Vegetable ink
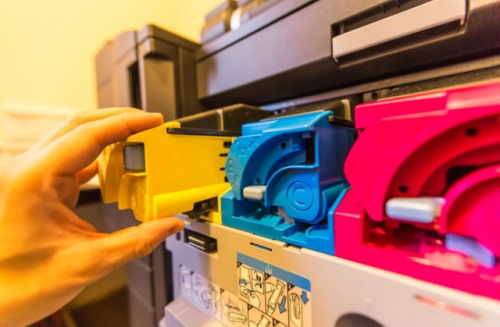
Vegetable ink
The three main components of ink are pigment, binder and additive.
Pigments provide color for ink; A binder is a wet substance that can disperse the pigment evenly, such as oil, water, soy or other vegetable oils; Additives such as paraffin and petroleum fractions help to dilute and improve the performance of the ink on the printing press.
Petroleum-based inks were widely used more than 50 years ago because of their rapid drying and high cost efficiency. But the fly in the ointment is that the drying process of this ink can cause damage to the environment. Petroleum-based inks not only use non-renewable resources, but also produce VOC during the drying process - causing environmental pollution and global climate.
Conductive silver ink
Not only is the demand for silver ink for traditional applications such as film switches and PCBS still solid, but a number of new applications are emerging that will bring new business revenue to silver ink manufacturers.
Nano-ink
With the increasing role of thermal sensitive flexible substrate, low temperature curing function will play a particularly important role. Nano ink has high conductivity and can cure at low temperature.
Epoxy screen printing ink
Conductive silver ink
Not only is the demand for silver ink for traditional applications such as film switches and PCBS still solid, but a number of new applications are emerging that will bring new business revenue to silver ink manufacturers.
Nano-ink
With the increasing role of thermal sensitive flexible substrate, low temperature curing function will play a particularly important role. Nano ink has high conductivity and can cure at low temperature.
Epoxy screen printing ink
Epoxy screen printing ink layer is uniform and bright, the pigment dispersion is good, the fineness is uniform, the mesh property is good, the leveling property is good, the polar substrate has excellent adhesion after curing, the coating film has high hardness, luster and good water resistance, weather resistance and chemical resistance.
(1) Add proper amount of diluent before use and stir well;
(2) Different types of ink please use special thinner;
(3) Test printing to confirm the requirements of mass production;
(4) Do a good job of removing grease and impurities on the surface of the printed material to promote the adhesion effect;
(5) screen or printed surface with static electricity, will cause the printing ink will have pinholes;
(6) Too high ambient humidity will affect the printing effect;
(7) products coating practical dry, before laminated shipment; After the completion of the operation remaining ink closed container seal;
Safety rules: No fireworks are allowed when printing ink and diluent are used and stored. Pay attention to the ventilation condition of the construction site and avoid direct contact with the skin. Wash with a lot of water in the entrance, nose, eyes and ears carelessly or ask the doctor directly.
Thermosetting ink
Thermosetting ink
Thermosetting ink, also known as plastic melting ink, plastic ink, resin ink, mainly composed of plasticizer and resin, and additives and color. Because it has to be heated to cure the characteristics, so in the printing without plugging the net, and can be wet wet continuous printing, greatly improve the production efficiency.
Thermosetting ink is a new generation of textile printing ink. Because of its many advantages, it has largely replaced the traditional printing materials in foreign countries. In addition to the use of cement and water pulp processing under the specified requirements of the printing house, most printing manufacturers have understood and used a large number of thermosetting ink to process high-precision products.