Management and efficiency improvement of printing equipment
Time:2023-04-06
Views:3280
Improve production skills
1. Spot color solution
In order to improve the visual effect of products and attract consumers‘ purchase desire, more and more designers use large-area color block pattern to upgrade the grade of packaging, and the application of spot color has been recognized and pursued by more and more printing buyers. For the printing plant, how to reduce the machine test color, establish an internal ink database, offline can be the customer want to show the color, and make timely correction according to the feedback, to contribute to the production capacity and loss of the machine, is every printing plant is looking forward to. Thus, spot color matching system came into being.
After the completion of ink data entry, the color matching system can pull out the spot color formula from the database in just a few seconds, and use the color developing instrument to develop the color offline, so as to make the color prediction. The LAB value of the color is measured by the color instrument, and compared with the target value data. According to the difference direction, the formula is fine-tuned to correct the data until the standard is reached. The color matching system greatly improves the formula generation efficiency of spot color, and can realize the accuracy of color prediction, and greatly reduces the number and time of printing on the machine. It is a spot color solution worthy of promotion.
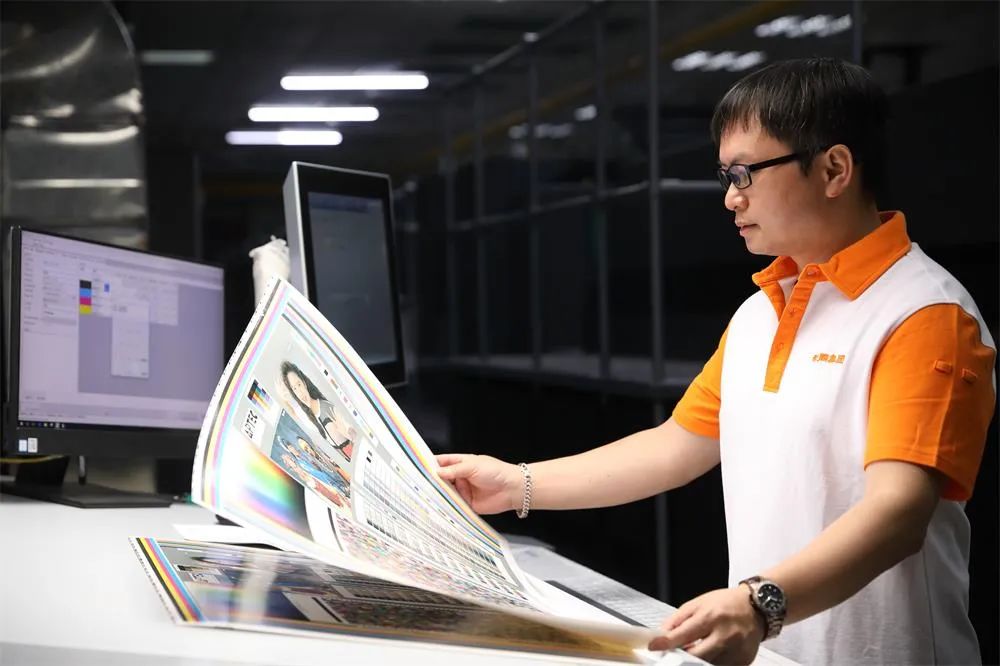
2. Establish a color management process
Although we use CIP3, closed loop technology, automatic cleaning system, etc., we have reduced preparation time and greatly increased efficiency. However, in the process of machine printing and color chasing, we still often encounter the printing and the customer‘s signature color is far from the situation, leading to the need to re-publish, correct the color, resulting in repeated machine color chasing predicament, greatly wasting the machine‘s production time.
To this end, the factory needs to make full use of color management techniques, standard digital proofing and standardized calibration of the press to establish an efficient pre-press printing process, which is necessary for efficiency and stable production quality.
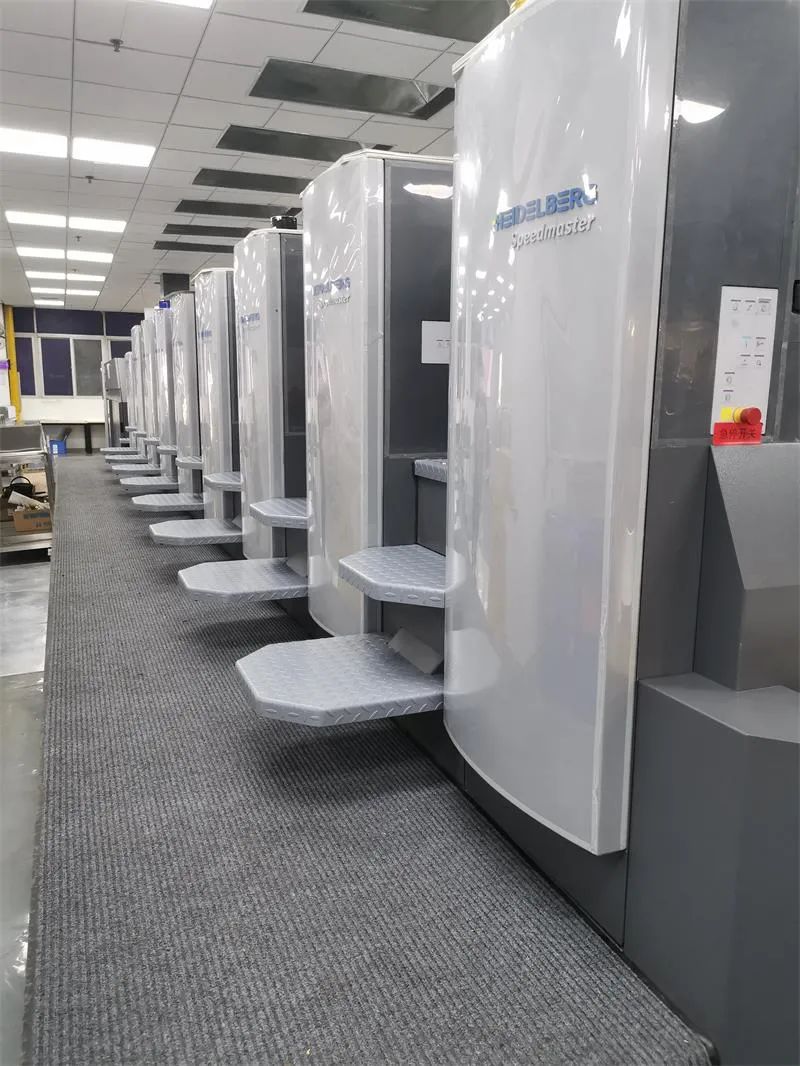
3. Material integration (ink, water and oil)
Packaging printing is a more complex and diversified process, and customers‘ requirements for packaging are also uneven and varied. To this end, we usually buy a variety of auxiliary materials with different technical parameters to put into production. For printing efficiency, the biggest impact is ink and water and oil.
Ink from the application can be divided into four color ink, special color base ink, halogen ink, halogen ink, mineral oil ink, vegetable oil ink, soybean oil ink, fast ink, low migration ink, fast drying ink, matte powder paper special ink, high light ink, high concentration ink, wide color range ink...... The application of water and oil is more extensive, including matte, wear resistance, folding resistance, touch, bronzing, reverse, UV bottom oil, ordinary bottom oil, wired, offline, explosion-proof color......
The above machine materials, in production if according to the requirements of the work order, frequent replacement, ink cleaning and water and oil cleaning is a great waste of time. Therefore, the best way is to be able to integrate the above two kinds of materials from the technology to the greatest extent. If it can be integrated into general materials suitable for production, it can greatly reduce the material replacement time in the production process of the machine, and make contributions to the output of the machine.
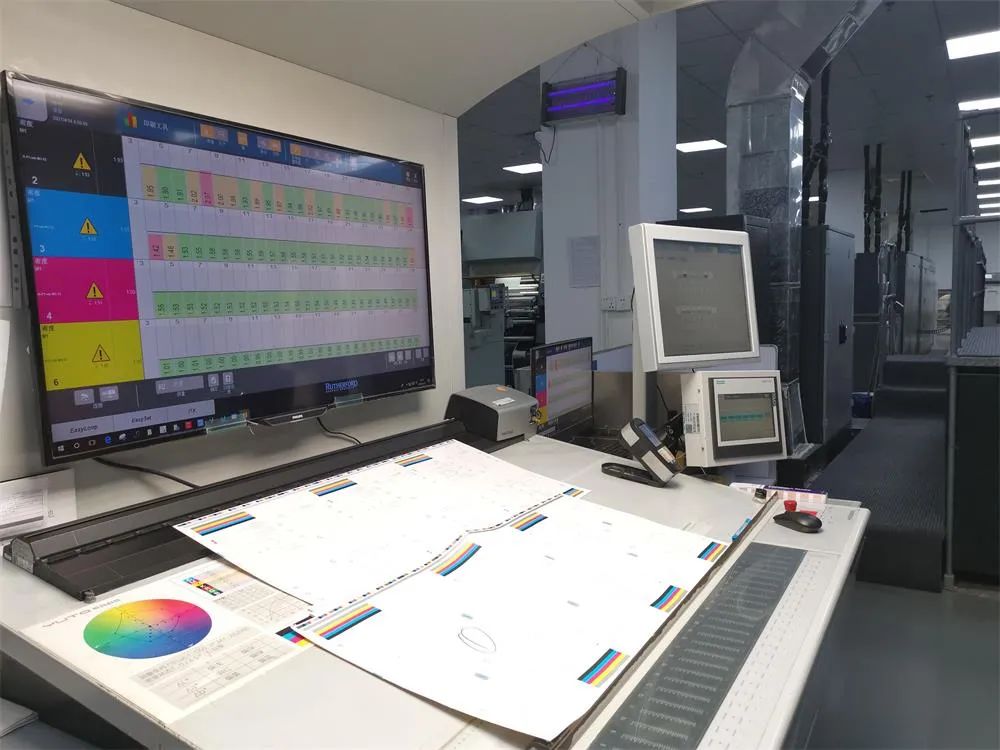
conclusion
There are many factors affecting the efficiency of the printing machine. Find the problems in time and formulate effective solutions; Improve the utilization rate of equipment through reasonable technical transformation; Introduce advanced practices in the industry to improve production skills; Fully mobilize the enthusiasm of employees, reasonable production scheduling, printing efficiency can be steadily improved.
In addition, the following points are very important to improve the efficiency of the equipment:
1) Establish a resource pool for equipment access, and try not to select more than three brands of equipment for each process. In this way, centralized and unified purchasing is greatly conducive to the management, maintenance and production scheduling of equipment, and thus conducive to the improvement of production efficiency.
2) Pay close attention to the professional ability of machine repair, establish the maintenance system of equipment (strict implementation of daily maintenance, weekly maintenance, monthly maintenance, annual maintenance), optimize the performance and state of equipment.
3) Each manufacturing enterprise will basically encounter production off-season, we can use this "precious" time, the equipment maintenance, annual overhaul and other work to do, so that the equipment to restore to the best state of operation, prepare for the arrival of the peak season.
4) It is particularly critical to build an efficient team with courage and high morale, and develop a set of people-oriented and effective incentive mechanism for overproduction according to the business structure.
5) In order to further stimulate the machine capacity, annual evaluation can be further developed, such as the top ten machine efficiency award, the highest single shift capacity award, the highest number of editions award, etc., to fully stimulate the machine morale of more work more gain.
Practice has proved that the significance of cultivating a professional equipment management team is not only to establish an efficient virtuous cycle improvement mechanism, carry out continuous optimization and promote lean production management, but more importantly, to enable our traditional packaging printing industry to strive towards the direction of standardization, standardization, automation, data and intelligence. Only in this way can enterprises achieve sustainable development.