Climate change causes ink to produce adhesion, blocking plate how to do?
Time:2024-11-04
Views:893
The humidity of the drying medium (air) has a great impact on the amount of residual solvent, once the moisture in the air enters the ink, it will cause the comprehensive volatility of the solvent to deteriorate and inhibit the volatilization of the solvent. The drying speed of the ink is generally delayed by nearly twice the ambient humidity, and it is also for this reason that the adhesion failure is most likely to occur when printing nylon film in the "Meiyu season", so in the high temperature and high humidity environment, the printing speed should be slowed down as much as possible to reduce the ink contact with the air to ensure that the ink can be fully dried.
When the temperature alternates between spring and summer, winter and spring, the formula of the printing solvent must be changed accordingly to reduce the phenomenon of ink blocking.
The general practice is to increase the content of slow drying (fast drying) solvent in the solvent; Accordingly, the process in the production, speed, exhaust should be adjusted accordingly to ensure that the solvent in the production is fully volatilized, if the ink in the slow drying (fast drying) solvent volatilization is not sufficient, it will produce a series of adverse effects: such as ink adhesion and anti-sticking, poor appearance in the composite, insufficient curing of the adhesive after composite. In the actual production, special attention should be paid to the area with shallow mesh in the printing pattern, because this area is the most prone to "blocking", and special circumstances can also be made in the pre-press plate making process changes to achieve "control in the first place, prevention first". Second is the control of ink viscosity. The stability of ink viscosity is related to the stability of printing hue, so when the temperature rises in summer and the solvent volatilization rate becomes faster, the closure of the ink circulation system is particularly important to reduce solvent volatilization and ensure the stability of ink viscosity. (3# measuring cup can be used to measure once every 30min)
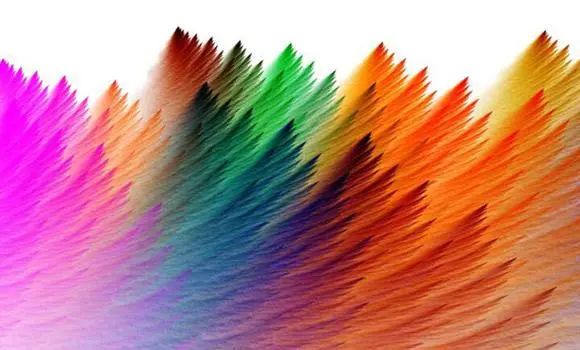
Distinguish between true and false solvents and adjust them
In the mixed solvent added to the printing ink, some solvents can dissolve the binder in the ink, called the true solvent, and some solvents can not dissolve the binder in the ink when used alone, called the false solvent. Due to the different volatilities between solvents, if the true solvent is volatilized first, the proportion of solvent in the ink will be destroyed, and the phenomenon of ink resin precipitation will occur. Therefore, the true solvent should be added in time, and when the solvent balance is poor, some true solvent with a slower evaporation rate should be added to maintain the balance of solvent volatility. Especially after the abolition of the use of benzene solvents such as methylene and xylene, the variety of solvents has increased, and many special solvents have been added to the four traditional solvent types. And various types of ink due to different ink resins, for the use of real solvents are also different, we must first find out which type of resin ink to use, in order to correspond to what kind of real solvent.
Different resins have different solvent release properties, and each binder has its own true solvent, sub-solvent and non-(false) solvent:
- The solubility of the solvent to the chlorinated polypropylene resin is in order: benzene > ketones > esters > alcohols.
- The solubility of solvent to polyurethane resin is in order of ketones > esters > benzenes.
- The solubility of the solvent to the polyamide resin is as follows: benzene > alcohol > ester > ketone.