5 reasons for overprinting
Time:2024-11-25
Views:822
Improper color sequence of printing
Multi-color printing by overprinting method, when the post-color ink is overprinted on the previous color ink, the adhesion between each other will be formed after rolling, and if the adhesion of the post-color ink is stronger than the adhesion of the previous color ink when separating, the post-color ink will stick the previous color ink away, resulting in poor overprinting of the print, resulting in "speckle". Therefore, to reasonably arrange the printing color order, generally in accordance with the four-color ink adhesion from large to small order, that is, in accordance with the order of black, magenta, green, yellow.
Improper ink absorption of paper
In multi-color printing, the ink transfer to the paper is carried out in a wet pressure wet state. If the ink absorption of the paper is too high, the linking material in the ink will penetrate too much into the inside of the paper, so that the oil in the ink layer is reduced, the pigment particles of the ink are suspended on the surface of the paper, resulting in a slower ink conjunctival speed, the lack of luster of the printing, and even sometimes the impression once the friction will occur. On the contrary, if the ink absorption of the paper is too low, the fixation speed of the ink is slow, the adsorption force is poor, and the previous color ink will stick off the previous color ink or the previous color ink will not be overprinted, resulting in poor overprinting of the printed product. Therefore, it is necessary to choose a paper with moderate ink absorption as far as possible, so that the ink fixation speed is moderate, the adhesion of the ink layer to the paper is moderate, and then the adhesion strength of the ink layer to the paper is increased.
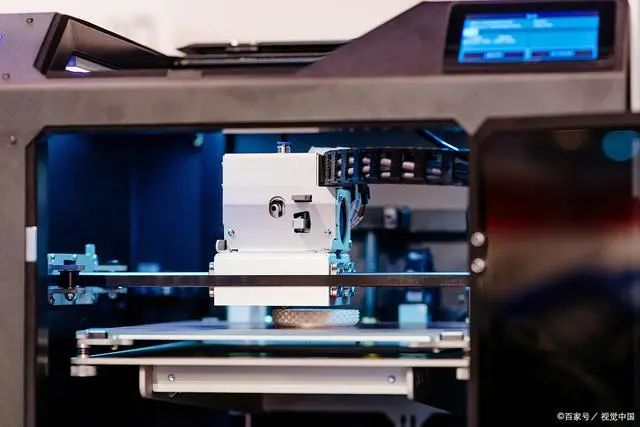
The pH value of the moistening solution is not properly controlled
If the pH value of the moistening solution is too low, the potion in the moistening solution will separate the binder and pigment in the ink, causing the ink to emulsify. When the ink is transferred to the paper, the pigment in the ink will float on the surface of the paper, and when the first color ink is overprinted before the first color ink, some pigments will be stuck away, resulting in poor overprinting of the printing product. Therefore, it is necessary to control the pH value of the moistening solution. Under normal circumstances, the pH value of the moistening solution should be controlled at 5.0 ~ 5.5.
Plate water supply is improper
The plate water supply is controlled by adjusting the contact pressure between the bucket roll and the metering roll. When the contact pressure between the bucket roller and the metering roller is small, the water supply of the plate is large, the water film formed is thicker, and the color of the ink film will become lighter, resulting in poor overprinting of the printed product; When the contact pressure between the bucket roller and the metering roller is large, the water supply of the plate is small, the water film formed is thinner, the ink film color will be darker, and the overprinting effect is better. Therefore, it is necessary to adjust the contact pressure between the bucket roller and the metering roller, so as to control the water supply of the plate, so that the water film thickness is moderate, so as to avoid poor overprinting of the printed product.
Crystallites are left on the surface of the roller
In multi-color printing, if some residual paper powder, moistening solution, and ink adhere to the surface of the ink roller, crystals will be produced on the surface of the ink roller, making the ink film on the ink roller difficult to control when separating, resulting in poor overprinting of the printing product. Therefore, it is necessary to regularly check whether the surface of the ink roller is smooth, and once the crystal is found, it must be removed in time.